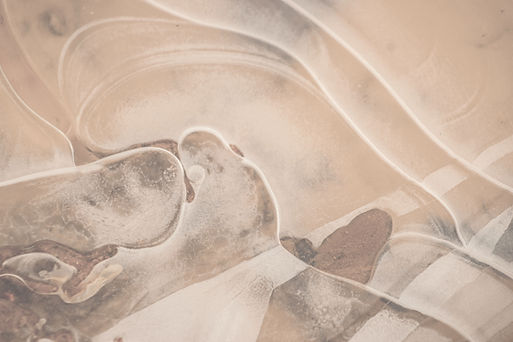
Honeywell Projects
This page documents the most important projects that I led during my 16-month co-op at Honeywell, where I worked as a process engineer. Unfortunately, I signed an NDA, which means I could not document the final prototypes, but I can describe what I created.
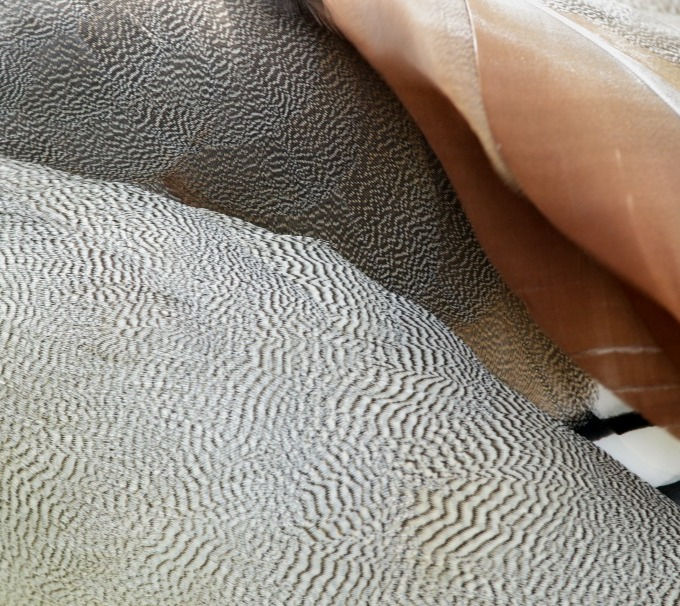
Sylgard Waste Automated Data Collection
I led the development of an automated data collection system focused on tracking Sylgard material waste throughout the aerospace manufacturing process. Sylgard, a high-cost silicone-based encapsulant, was previously monitored through manual logging, which often resulted in inaccurate records and limited traceability.
To solve this, I developed and implemented a Python-based automation tool that interfaced with operator input forms to record material usage and waste in real time. The script parsed and organized the data, then automatically updated a centralized database, significantly reducing human error and improving data accessibility for engineers and managers.
This solution enhanced inventory tracking, supported lean manufacturing goals by reducing material waste, and enabled deeper insight into process inefficiencies. It also served as a foundation for future integration with predictive maintenance and quality control systems.

Customized Versatile Transport Lift
In response to a workplace injury caused by manual handling of heavy aerospace units, I led the design and development of a Customized Versatile Transport Lift at Honeywell. The goal was to create a safe, ergonomic solution for transporting and positioning large, irregularly shaped components.
I designed a lift equipped with articulating arms capable of adjusting to various unit geometries, enabling operators to securely grasp and transport parts with minimal physical strain. The lift design prioritized modularity and ease of use, with a mechanical structure that allowed quick reconfiguration for different product lines.
The project involved cross-functional collaboration with operators, safety experts, and mechanical engineers to ensure compliance with ergonomic standards and production requirements. This solution significantly reduced the risk of injury, improved operational efficiency, and served as a scalable model for similar applications across the manufacturing floor.

Robotic Arm for Unit Transport to CMM
To improve safety and precision in the handling of sensitive aerospace components, I led the development of a pneumatically powered robotic arm designed to transfer large units from transport carts to a Coordinate Measuring Machine (CMM) for quality inspection.
The pneumatic system was developed in collaboration with a third-party vendor, where I was responsible for communicating technical requirements, evaluating feasibility, and negotiating quotes. I designed the terminal arm in-house using UHMW PTFE to ensure a non-marring surface and integrated adjustable arms capable of safely gripping components of various sizes without damaging their surfaces. The design enabled precise, repeatable placement of parts on the CMM, reducing manual handling risks and improving inspection throughput.
This project combined mechanical design, vendor coordination, and safety-focused innovation to deliver a customized automation solution that enhanced both operator safety and quality control accuracy.
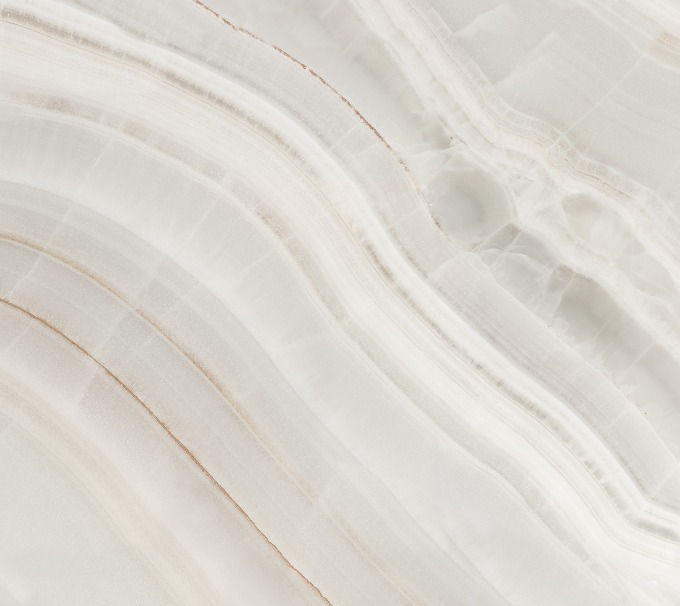
Custom Collet For Sensor Sanding
To improve operator safety and precision during sensor sanding, I designed and 3D-printed a custom collet capable of securely gripping circular sensors of varying diameters. The collet was fitted with a ball bearing, allowing the sensor to spin freely during sanding while keeping operators’ hands at a safe distance from the sanding belt.
This solution reduced the risk of hand injuries, improved ergonomic workflow, and enhanced consistency by enabling smoother and more controlled rotation of the sensors. The design’s self-centering feature accommodated batch-to-batch variability and helped reduce material waste due to more uniform finishing.